第 1 章 绪论
1.1 研究的目的及意义
1.1.1 研究目的
近年来,伴随着我国在航空航天、汽车制造等工业领域的发展,给锻造行业注入了新的生机与活力。为了满足“精密、环保、高效”的市场需求,以热冷复合成形技术为代表的近净成形技术正在被迅速推广。近净成形理念是追求零件在生产过程中具备高精度、高性能、低能耗、少无再加工等要素,是未来锻造行业必然发展的趋势[1-4]。
突缘类零件作为汽车工业、装备制造、航空航天、动力工业等重要领域中不可缺少的关键零部件之一,如用于传动装置的分动箱突缘叉、用于减速装置的减速器突缘、用于连接装置的管端突缘、三脚突缘、角齿突缘等。突缘类零件形状复杂,使用工况多变,整体质量要求高。目前有多种生产方式应用于突缘类零件的制造,主要的工艺方式有:铸造、机加工及热模锻造。采用铸造不仅铸造件的机械性能低而且易产生缩孔、裂纹、晶粒粗细不均等缺陷。采用机加工方式不仅会破坏材料纤维造成承载力降低,而且材料浪费严重。采用热模锻造不仅易产生氧化,而且在降温时产生冷缩现象,影响锻件的表面平整度。所以,传统的成形工艺方式不仅生产周期长、成本高,而且容易造成内部组织不均、纤维断裂、晶粒粗大等缺陷,从经济效益或品质上都已经无法满足工业发展的需求。因此,伴随着新工艺、新技术、新设备的开发,大量的学者采用复合工艺对金属体积成形方法进行深入研究[5-9]。
突缘类零件作为汽车工业、装备制造、航空航天、动力工业等重要领域中不可缺少的关键零部件之一,如用于传动装置的分动箱突缘叉、用于减速装置的减速器突缘、用于连接装置的管端突缘、三脚突缘、角齿突缘等。突缘类零件形状复杂,使用工况多变,整体质量要求高。目前有多种生产方式应用于突缘类零件的制造,主要的工艺方式有:铸造、机加工及热模锻造。采用铸造不仅铸造件的机械性能低而且易产生缩孔、裂纹、晶粒粗细不均等缺陷。采用机加工方式不仅会破坏材料纤维造成承载力降低,而且材料浪费严重。采用热模锻造不仅易产生氧化,而且在降温时产生冷缩现象,影响锻件的表面平整度。所以,传统的成形工艺方式不仅生产周期长、成本高,而且容易造成内部组织不均、纤维断裂、晶粒粗大等缺陷,从经济效益或品质上都已经无法满足工业发展的需求。因此,伴随着新工艺、新技术、新设备的开发,大量的学者采用复合工艺对金属体积成形方法进行深入研究[5-9]。
目前,为了确定成形工艺方案的合理性,传统的“试错法”生产模式逐渐被计算机仿真模拟技术所代替。计算机仿真模拟技术可以很好的解决实际实验难点问题,简化试验过程,节约成本与时间,预测金属塑性成形过程中存在的缺陷与不足,其优势已在金属塑性成形的研究中广泛应用[10,11]。我国在突缘类零件的研究和制造方面获得了大量的成果,而对复杂突缘类零件的模拟研究较少。所以,本文通过研究突缘类件成形过程中的成形机理和临界条件,实现对突缘类件的成形过程进行有效控制,采用有限元数值模拟技术对突缘类件成形工艺过程进行一系列的相关研究。
...........................
1.2 热冷复合成形工艺简介及发展现状
1.2.1 热冷复合成形工艺简介
随着“低碳经济”理念的不断推行,热冷复合成形工艺在节能、减排、增效等方面比传动机械制造技术具有较大的优势,受到广大汽车零配件制造商们的青睐,因而热冷复合成形工艺成为了国内外锻造行业研究学者的一个重要研究方向[16-18]。 热冷复合成形工艺是热挤和冷挤相结合的成形工艺,先通过热挤或温挤基本成形,再通过冷挤压最终成形[19]。热冷复合成形工艺是将两种不同的成形工艺组合在一起,以热挤压件作为冷挤压工步的毛坯,使其充分发挥各自的优点,进而达到最佳的成形效果,其技术特点如表 1.1 所示[20]。
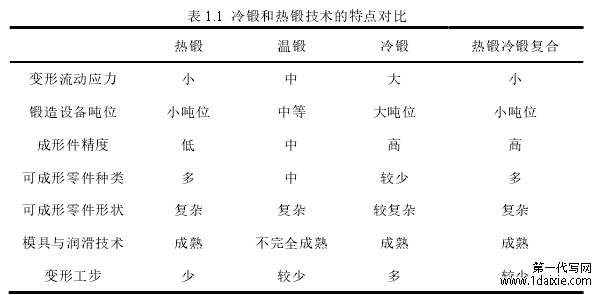
采用热冷复合工艺,可扬长避短,将热挤压与冷挤压的优势互补,适合生产外形相对复杂,精度要求高的轴对称或旋转对称的突缘类、杯杆类等零件。此外,其冲击性能尤其是低温冲击性能明显优于热模锻,由此可以带来比热模锻技术和机械切削加工技术要高的附加值和生产利润,是未来锻造成形技术发展的重要研究方向。
.........................
...........................
1.2 热冷复合成形工艺简介及发展现状
1.2.1 热冷复合成形工艺简介
随着“低碳经济”理念的不断推行,热冷复合成形工艺在节能、减排、增效等方面比传动机械制造技术具有较大的优势,受到广大汽车零配件制造商们的青睐,因而热冷复合成形工艺成为了国内外锻造行业研究学者的一个重要研究方向[16-18]。 热冷复合成形工艺是热挤和冷挤相结合的成形工艺,先通过热挤或温挤基本成形,再通过冷挤压最终成形[19]。热冷复合成形工艺是将两种不同的成形工艺组合在一起,以热挤压件作为冷挤压工步的毛坯,使其充分发挥各自的优点,进而达到最佳的成形效果,其技术特点如表 1.1 所示[20]。
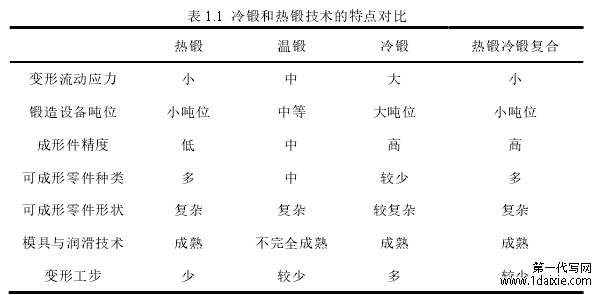
采用热冷复合工艺,可扬长避短,将热挤压与冷挤压的优势互补,适合生产外形相对复杂,精度要求高的轴对称或旋转对称的突缘类、杯杆类等零件。此外,其冲击性能尤其是低温冲击性能明显优于热模锻,由此可以带来比热模锻技术和机械切削加工技术要高的附加值和生产利润,是未来锻造成形技术发展的重要研究方向。
.........................
第 2 章 突缘类件成形工艺方案研究及其数值模拟分析
2.1 引言
根据突缘类零件的结构特点不同,产生了不同的生产工艺方案。对于大多数突缘类零件的成形过程采用一次加热连续成形的方式,这种方式造成锻件表面平整度低、氧化严重、材料浪费严重等现象。本章主要对突缘类锻件的成形工艺方案进行归纳总结,并提出采用热冷复合成形工艺方案的研究思路,设计两种不同的成形工艺方案。以三脚突缘为研究对象,利用 DEFORM 有限元软件模拟了两种成形工艺方案的终成形阶段,通过比较两种成形方案在终成形阶段的成形载荷、等效应力应变、温度场,选择较优的成形工艺方案,其结果对突缘类件的成形工艺选择具有一定的参考指导作用。
2.1 引言
根据突缘类零件的结构特点不同,产生了不同的生产工艺方案。对于大多数突缘类零件的成形过程采用一次加热连续成形的方式,这种方式造成锻件表面平整度低、氧化严重、材料浪费严重等现象。本章主要对突缘类锻件的成形工艺方案进行归纳总结,并提出采用热冷复合成形工艺方案的研究思路,设计两种不同的成形工艺方案。以三脚突缘为研究对象,利用 DEFORM 有限元软件模拟了两种成形工艺方案的终成形阶段,通过比较两种成形方案在终成形阶段的成形载荷、等效应力应变、温度场,选择较优的成形工艺方案,其结果对突缘类件的成形工艺选择具有一定的参考指导作用。
突缘类锻件是属于带孔轴对称或旋转对称结构,例如汽车上的一些关键零件传动轴突缘叉、滑动叉、三爪突缘、套管叉、深孔突缘、万向节叉、法兰突缘、三脚突缘等都属于突缘类典型零件[37-44]。大多数零件具有薄壁、小截面且局部形状相对复杂的特点,这些特点造成了零件的加工难易程度不同。同时,突缘类零件多用于汽车的关键部位,要求具有较好的力学性能,才能长期保证汽车的稳定性,所以有必要对突缘类件的成形工艺进行深入的研究。
.......................
2.2.1 突缘类件成形工艺方案的分析
本小节对具有代表性的突缘类锻件根据对结构特点、原工艺方案、缺陷、改进方法、改进后技术效果等方面进行总结,在大量查阅相关资料的基础上将其各自的特点列于表 2.1 中。
从表 2.1 中可以得出,突缘类锻件是带孔的轴对称或旋转对称结构,一般轴对称突缘类锻件的盘部扁平,杆部呈耳状凸起或通孔;旋转对称突缘类锻件的盘部呈枝杈状,杆部为通孔。
根据零件的结构不同,锻件成形过程中存在着一系列的缺陷:
(1)充型不满,生产效率低;
(2)材料利用率低,产生飞边量大,造成机加工量大;
(3)管壁产生折叠,模具磨损严重。 根据表 2.1 所总结的突缘类成形工艺方案可以清晰的比较出成形工艺方案的相同之处:(1)采用预成形+终成形的成形工艺方案;(2)采用连续热模锻成形工艺。不同之处:(1)采用开式模锻必然造成飞边量大,材料浪费严重;(2)一次挤压成形工艺易造成填充不满的缺陷;(3)为了充型良好,预成形前存在金属分流,达到体积预分配的目的,即制坯阶段。当分叉数目多、高度方向尺寸大时,直接从坯料到预成形过程容易造成充型不满、折叠等现象。
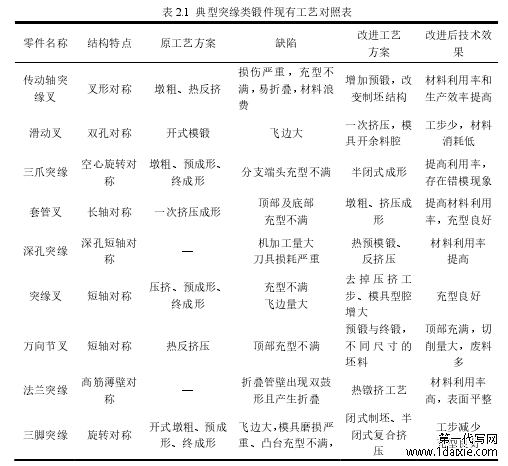
............................
.......................
2.2.1 突缘类件成形工艺方案的分析
本小节对具有代表性的突缘类锻件根据对结构特点、原工艺方案、缺陷、改进方法、改进后技术效果等方面进行总结,在大量查阅相关资料的基础上将其各自的特点列于表 2.1 中。
从表 2.1 中可以得出,突缘类锻件是带孔的轴对称或旋转对称结构,一般轴对称突缘类锻件的盘部扁平,杆部呈耳状凸起或通孔;旋转对称突缘类锻件的盘部呈枝杈状,杆部为通孔。
根据零件的结构不同,锻件成形过程中存在着一系列的缺陷:
(1)充型不满,生产效率低;
(2)材料利用率低,产生飞边量大,造成机加工量大;
(3)管壁产生折叠,模具磨损严重。 根据表 2.1 所总结的突缘类成形工艺方案可以清晰的比较出成形工艺方案的相同之处:(1)采用预成形+终成形的成形工艺方案;(2)采用连续热模锻成形工艺。不同之处:(1)采用开式模锻必然造成飞边量大,材料浪费严重;(2)一次挤压成形工艺易造成填充不满的缺陷;(3)为了充型良好,预成形前存在金属分流,达到体积预分配的目的,即制坯阶段。当分叉数目多、高度方向尺寸大时,直接从坯料到预成形过程容易造成充型不满、折叠等现象。
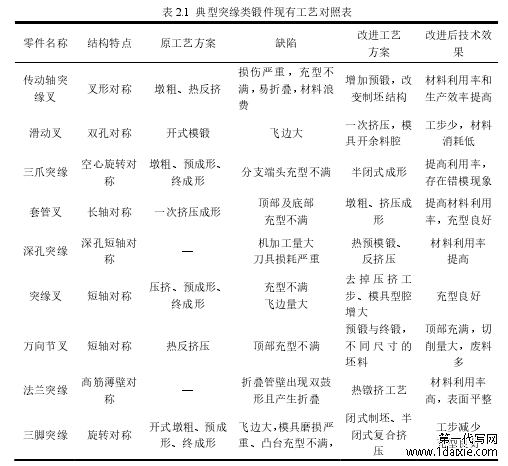
............................
第 3 章 三脚突缘件成形过程的数值模拟 .......................................... 20
3.1 引言 ................................ 20
3.2 三脚突缘成形工艺流程的确定 ................................... 20
3.3 三脚突缘锻件图设计及相关要素的确定 ........................... 21
第 4 章 基于响应面法的三脚突缘成形工艺参数优化 ......................... 39
4.1 引言 ............................... 39
4.2 响应面法简介 ................................... 39
第 5 章 三脚突缘成形过程模具优化 ...................................... 56
5.1 引言 ............................... 56
5.2 终成形凸模过渡圆角优化 ................................. 56
第 5 章 三脚突缘成形过程模具优化
5.1 引言
本文的三脚突缘成形过程中,制坯和预成形过程均采用热挤压成形方式,金属流动性相对较好,成形载荷较小,所以仅对终成形过程的磨损情况进行模具结构优化。依据第三章所研究的终成形模具模损分析,凸模磨损量比凹模磨损量大,且主要磨损区域位于过渡圆角部位,因此,本章针对终成形凸模模具的过渡处圆角半径进行优化。最后,根据三脚突缘的成形工艺过程所设计的锻件图,设计合理的预成形与终成形模膛和整体模具结构。同时,对本文所涉及的成形工艺研究及模具设计进行经费预算,
5.1 引言
本文的三脚突缘成形过程中,制坯和预成形过程均采用热挤压成形方式,金属流动性相对较好,成形载荷较小,所以仅对终成形过程的磨损情况进行模具结构优化。依据第三章所研究的终成形模具模损分析,凸模磨损量比凹模磨损量大,且主要磨损区域位于过渡圆角部位,因此,本章针对终成形凸模模具的过渡处圆角半径进行优化。最后,根据三脚突缘的成形工艺过程所设计的锻件图,设计合理的预成形与终成形模膛和整体模具结构。同时,对本文所涉及的成形工艺研究及模具设计进行经费预算,
为后续的实际生产提供一定的理论依据。
预成形工步尺寸是依据终成形工步图所设计,并增加挤压件收缩率,从而确定预成形模具的相关尺寸。在对预成形模膛进行设计时,必须注意以下几点[60]:
(1)为了使金属在终成形时以镦粗方式充满模膛,预成形件高度尺寸应比终成形件高出 2~5mm;水平尺寸应适当减小,但预成形件横截面面积比终成形件相应截面面积要大一些。
(2)应严格控制预成形件各部位体积,设计合理的多余金属能在终成形时稳定流向,避免锻件内部出现回流、折叠、缩孔等缺陷。
(3)应考虑预成形件在终成形模中的定位问题。因此,预成形工步图中某些部位的形状和尺寸应与终成形件基本吻合,以避免因锻件放偏导致充型不满和金属过剩现象的发生。
............................
第 6 章 总结与展望预成形工步尺寸是依据终成形工步图所设计,并增加挤压件收缩率,从而确定预成形模具的相关尺寸。在对预成形模膛进行设计时,必须注意以下几点[60]:
(1)为了使金属在终成形时以镦粗方式充满模膛,预成形件高度尺寸应比终成形件高出 2~5mm;水平尺寸应适当减小,但预成形件横截面面积比终成形件相应截面面积要大一些。
(2)应严格控制预成形件各部位体积,设计合理的多余金属能在终成形时稳定流向,避免锻件内部出现回流、折叠、缩孔等缺陷。
(3)应考虑预成形件在终成形模中的定位问题。因此,预成形工步图中某些部位的形状和尺寸应与终成形件基本吻合,以避免因锻件放偏导致充型不满和金属过剩现象的发生。
............................
6.1 总结
突缘类产品是变速器、驱动桥的重要组成零部件,仍占据着汽车、飞机等工业市场的主导地位。然而传统的生产工艺及模具设计面临着新技术新工艺的冲击,尤其是生产工艺过程亟需进行革新。本文结合使用有限元数值模拟技术和响应面法,对突缘类产品的生产工艺进行分析,并以典型突缘件三脚突缘作为研究对象,分析热冷复合技术在突缘类产品生产中的应用研究。同时,通过响应面法对生产过程的工艺参数进行优化,最终获得最优工艺参数组合为实际生产提供理论指导。本文的研究结果主要包括以下几点:
(1)本文通过分析传统的突缘类生产工艺,提出突缘类件锻造采用热冷复合成形工艺方案的思路。以典型突缘件三脚突缘为研究对象,运用有限元软件对两种成形工艺方案进行数值模拟,对终成形过程的成形载荷、损伤因子、折叠角、温度场进行对比分析,确定热冷复合挤压成形工艺的可行性。
(2)通过分析三脚突缘的结构特点,确定三脚突缘成形过程的工艺技术路线。根据三脚突缘的零件图结合体积成形原则确定相关要素,作出制坯、预成形、终成形过程的二维图。运用有限元软件对制坯、预成形、终成形过程进行数值模拟分析,并对终成形过程的模具磨损程度分析。
(3)结合响应面试验设计法对三脚突缘锻件的成形过程进行了数值模拟分析。 在预成形阶段,利用中心组合设计方法(CCD)对影响因素的取值范围进行试验设计,以成形载荷和凸模具磨损为评价指标对预成形过程的工艺参数设计 30 组搭配方案,对比 30 组搭配组合的模拟结果并确定四组较优工艺参数组合,并对四组方案的实际值与预测值的误差对比分析,确定了预成形过程的最优工艺参数组合。
在终成形阶段,利用 BOX 设计方法对影响因素的取值范围进行试验设计,以成形载荷和凸模具磨损为评价指标对终成形成形过程的工艺参数设计 17 组搭配方案,对比 17 组搭配组合的模拟结果并确定两组较优工艺参数组合,并对两组方案的实际值与预测值的误差对比分析,确定了终成形过程的最优工艺参数组合。
在终成形阶段,利用 BOX 设计方法对影响因素的取值范围进行试验设计,以成形载荷和凸模具磨损为评价指标对终成形成形过程的工艺参数设计 17 组搭配方案,对比 17 组搭配组合的模拟结果并确定两组较优工艺参数组合,并对两组方案的实际值与预测值的误差对比分析,确定了终成形过程的最优工艺参数组合。
(4)根据 3.4 节中终成形成形过程模具磨损分析,对三脚突缘终成形过程中凸模过渡圆角 A 处的圆角半径优选 4 组(3mm、4mm、5mm、6mm)进行数值模拟,综合对比分析模拟结果,确定较优的圆角半径为 4mm。其次,主要对三脚突缘的预成形和终成形过程的凹、凸模型腔进行三维建模。并对三脚突缘模具进行整体设计,设计出适合突缘类闭式锻造的通用模具。
参考文献(略)
参考文献(略)