第一章 绪论
1.1 研究的背景、目的和意义
1.1.1 研究背景
近年来,制造企业迫于发展和提高经济效益的压力,逐渐认识到加强信息化建设的的重要性。然而,生产管理系统和设备终端控制管理系统在实际的制造企业信息化建设中,是作为不同领域的系统分别构建的,因此在系统构建完成后,实际上是两套独立的系统。而在实际操作过程中,企业要求将ERP等生产管理系统的工作单据直接发送到设备的终端控制系统。同时,对于生产管理系统,也希望通过采集数控终端设备的相关数据,实现设备状态和生产过程的控制,实时监控并能及时响应生产过程中的生产异常。为了满足这一需求,企业希望在管理系统和设备管控系统之间建立良好的联系,有效地实现数据的传输和共享。
1.1 研究的背景、目的和意义
1.1.1 研究背景
近年来,制造企业迫于发展和提高经济效益的压力,逐渐认识到加强信息化建设的的重要性。然而,生产管理系统和设备终端控制管理系统在实际的制造企业信息化建设中,是作为不同领域的系统分别构建的,因此在系统构建完成后,实际上是两套独立的系统。而在实际操作过程中,企业要求将ERP等生产管理系统的工作单据直接发送到设备的终端控制系统。同时,对于生产管理系统,也希望通过采集数控终端设备的相关数据,实现设备状态和生产过程的控制,实时监控并能及时响应生产过程中的生产异常。为了满足这一需求,企业希望在管理系统和设备管控系统之间建立良好的联系,有效地实现数据的传输和共享。
1990年,美国先进制造业研究院(AMR)组织相关研究工作,以满足制造业的相关需求为目的,提出制造执行系统(MES)的概念。它在生产管理系统和终端设备控制系统之间建立了强有力的联系。通过这一环节,可以有效地实现管理系统和控制系统的数据传输和共享。同时,加强车间生产的管理和控制,解决生产管理系统与设备控制系统的有效沟通问题。实践中提倡制造业用三层模型来代表信息化。这三个层次包括企业级(ERP)、生产级(MES)和过程级(PLC)。阐明了制造执行系统在企业总体信息中的地位和重要作用。MES的实际位置处于企业资源计划(ERP)和过程控制系统PLC的中间。ERP作为企业管理系统即企业资源计划,PLC是可编程控制系统,而MES是生产执行系统。对于不同类别的制造企业,制造执行系统的应用特点也不同。因此,在制造企业中,为了满足企业发展的需要,MES系统已经在整个业界中得到实施,逐渐成为企业发展的突破口。
......................
1.2 国内外研究现状及发展趋势
1.2.1 国外研究现状
在本世纪初,风险管理以系统学科方式,出现在西方工业国家,它以 1915年德国学者勒特纳的《企业风险理论》为标志。至 1963 年,美国出版了名为《企业风险管理》的书籍,引起欧美国家的关注。从那时起,风险管理开始以独立学科的形式出现,对其进行的研究也更加系统和专业。Aven[1]等人针对学科界对风险的两类普遍定义,他们通过深入研究认为,目前对于风险的定义只是将其视为一种状态,无法得出风险高低,因此当面对不同风险的时候很难做出选择,他们建议对风险定义进行重新表述:风险是某项活动后果严重性和不确定性,严重程度取决于人们对其的评价。
软件项目风险管理是以软件工程知识库为基础的。是一门通过一定的方法、过程和工具,不断地对开发过程中会带来的异常(风险)进行预评估,并决定需要处理哪些风险以及产生相应处理策略的学科[2]。这一理论与实践相结合的研究领域正在不断地变化与发展,但同时也显示出巨大的社会效益和经济效益,因此越来越受到业界的重视。
理论方面,《软件风险管理》一书的作者Boehm被公认为是信息科技风险管理领域的奠基人,在同时期,Charette结合基础理论又拓展了一个多角度的风险管理架构[2]。沃尔什和其他人认为决策者极大地影响了项目的成败,风险管理不但要考虑方法还要充分考虑干预人的影响[3]。Michael S. Gibson 认为,制造企业风险管理应当在当下信息时代发展的有利背景下,充分整合资源,集中提升管理水平,改变过去零散的风险管理方式,实现集权管理[4]。Tarazi [5]采用实证分析法对VAR(风险价值)模型开展研究,在对欧洲的一些大型制造企业进行实地走访和网络调查后,否定了软件开发项目的高风险与项目运营活动的高占比存在必然的联系。而美国软件工程协会(SEI)对软件项目风险管理定义的五个阶段:识别、分析、应对计划、跟踪与控制是目前最主流和被应用最为广泛的风险管理理论[6]。
.........................
第二章 相关理论与方法
2.1 项目管理的概念
在《PMBOK 指南》(第 5 版)中,美国项目管理协会将项目定义为“创造独特产品、服务或结果的临时工作”,项目管理定义为“将知识、技能、工具和技术应用于项目活动以满足项目要求”。项目管理知识域和过程组见表 2.1 所示。
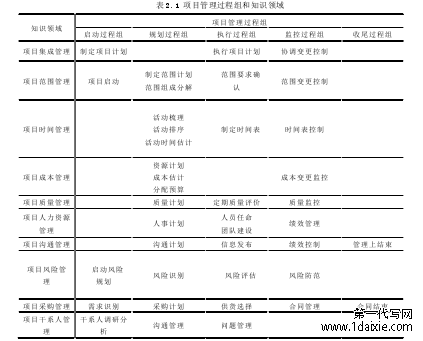
由表 2.1 可知,项目管理包含了十项知识领域和五项过程组。启动过程组是在项目初次启动时或项目的某个阶段启动时的一系列过程,包括项目立项范围、金额、内部和外部利益关系者、选择项目经理,并在项目章程和利益相关者登记册中明确上述信息。规划过程组是逐步确定项目管理的计划阶段,包括定义项目范围、规划项目活动和时间、项目成本预算、采购计划和人事计划的编制,质量和风险计划的控制等等。其结果是输出各项内容的管理计划。执行过程组是对计划的实施工作,用以检查计划的完善和指标的正确性,同时还包含了执行已被批准的变更。在这个过程中,问题日志或经验教训库开始被建立,相关计划和指标的缺陷被纠正。监控过程组是跟踪、审查和报告整体项目进展的过程,是实现项目目标的手段之一,主要作用是让相关方了解项目目前的状态以及预测未来的状态,起到监督和指导的作用。收尾过程组是在项目或阶段完成后实施一系列工作,如验收、项目资源发放、记录经验教训、项目后评价、合同收尾等,并将成果递交给其他人。五个过程组之间的关系和十大知识域见表 2.1 所示。
2.2.1 MES 的基本概念
Manufacturing Execution System(生产制造执行系统)简称:MES,是美国管理界上世纪 90 年代的新概念,是生产制造过程实现车间生产敏捷化的基本技术手段。
NIST(美国国家标准研究所)对 MES 的定义是:收集硬件和软件的数据和状态信息,以优化从接受订单到最终产品制造的整个过程中的管理活动。
国际制造执行系统协会对 MES 的描述是,为实现快速生产和及时响应,包括提高设备利用率、降低库存、提升质量能力、增加经营效益等目标,该系统对所有生产活动中的所有生产环节因素,包括人员、设备、产品等进行实时、不间断、准确的数据通信,并通过预设的流程或逻辑指导产品生产、人机管理和工厂运作。该系统的重点是优化和改善生产活动,减少浪费,提高经济效益。其关键词是精确的实时数据,而这一点是基于事务的 ERP 和 MRP-II 系统没有考虑到的。 从上面可以看出,关于 MES 虽然描述不一,但是核心内容不尽相同:
(1)MES 可以在企业各个信息终端实现双向通信,管理层可以修改和下达逻辑指令到控制层,同样,控制层可以根据预设的需要将生产数据信息实时存储到数据库,用以数据查询、比对和分析。
(2)MES 有较强的及时性,这是系统的核心,抛开这一特点,MES 将毫无价值。这是实现企业动态管理的基础。
(3)MES 数据的准确性是优化和改善活动的基础,这就要求系统的数据库搭建逻辑缜密,生产活动无漏洞,数据传输无差错。
...............................
第三章 KBD 公司 MES 项目实施背景分析 .......................... 15
3.1 汽车零部件制造企业的现状 ........................................... 15......................
1.2 国内外研究现状及发展趋势
1.2.1 国外研究现状
在本世纪初,风险管理以系统学科方式,出现在西方工业国家,它以 1915年德国学者勒特纳的《企业风险理论》为标志。至 1963 年,美国出版了名为《企业风险管理》的书籍,引起欧美国家的关注。从那时起,风险管理开始以独立学科的形式出现,对其进行的研究也更加系统和专业。Aven[1]等人针对学科界对风险的两类普遍定义,他们通过深入研究认为,目前对于风险的定义只是将其视为一种状态,无法得出风险高低,因此当面对不同风险的时候很难做出选择,他们建议对风险定义进行重新表述:风险是某项活动后果严重性和不确定性,严重程度取决于人们对其的评价。
软件项目风险管理是以软件工程知识库为基础的。是一门通过一定的方法、过程和工具,不断地对开发过程中会带来的异常(风险)进行预评估,并决定需要处理哪些风险以及产生相应处理策略的学科[2]。这一理论与实践相结合的研究领域正在不断地变化与发展,但同时也显示出巨大的社会效益和经济效益,因此越来越受到业界的重视。
理论方面,《软件风险管理》一书的作者Boehm被公认为是信息科技风险管理领域的奠基人,在同时期,Charette结合基础理论又拓展了一个多角度的风险管理架构[2]。沃尔什和其他人认为决策者极大地影响了项目的成败,风险管理不但要考虑方法还要充分考虑干预人的影响[3]。Michael S. Gibson 认为,制造企业风险管理应当在当下信息时代发展的有利背景下,充分整合资源,集中提升管理水平,改变过去零散的风险管理方式,实现集权管理[4]。Tarazi [5]采用实证分析法对VAR(风险价值)模型开展研究,在对欧洲的一些大型制造企业进行实地走访和网络调查后,否定了软件开发项目的高风险与项目运营活动的高占比存在必然的联系。而美国软件工程协会(SEI)对软件项目风险管理定义的五个阶段:识别、分析、应对计划、跟踪与控制是目前最主流和被应用最为广泛的风险管理理论[6]。
.........................
第二章 相关理论与方法
2.1 项目管理的概念
在《PMBOK 指南》(第 5 版)中,美国项目管理协会将项目定义为“创造独特产品、服务或结果的临时工作”,项目管理定义为“将知识、技能、工具和技术应用于项目活动以满足项目要求”。项目管理知识域和过程组见表 2.1 所示。
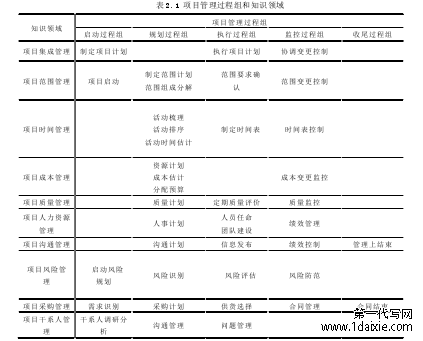
由表 2.1 可知,项目管理包含了十项知识领域和五项过程组。启动过程组是在项目初次启动时或项目的某个阶段启动时的一系列过程,包括项目立项范围、金额、内部和外部利益关系者、选择项目经理,并在项目章程和利益相关者登记册中明确上述信息。规划过程组是逐步确定项目管理的计划阶段,包括定义项目范围、规划项目活动和时间、项目成本预算、采购计划和人事计划的编制,质量和风险计划的控制等等。其结果是输出各项内容的管理计划。执行过程组是对计划的实施工作,用以检查计划的完善和指标的正确性,同时还包含了执行已被批准的变更。在这个过程中,问题日志或经验教训库开始被建立,相关计划和指标的缺陷被纠正。监控过程组是跟踪、审查和报告整体项目进展的过程,是实现项目目标的手段之一,主要作用是让相关方了解项目目前的状态以及预测未来的状态,起到监督和指导的作用。收尾过程组是在项目或阶段完成后实施一系列工作,如验收、项目资源发放、记录经验教训、项目后评价、合同收尾等,并将成果递交给其他人。五个过程组之间的关系和十大知识域见表 2.1 所示。
............................
2.2 MES 的基本理论2.2.1 MES 的基本概念
Manufacturing Execution System(生产制造执行系统)简称:MES,是美国管理界上世纪 90 年代的新概念,是生产制造过程实现车间生产敏捷化的基本技术手段。
NIST(美国国家标准研究所)对 MES 的定义是:收集硬件和软件的数据和状态信息,以优化从接受订单到最终产品制造的整个过程中的管理活动。
国际制造执行系统协会对 MES 的描述是,为实现快速生产和及时响应,包括提高设备利用率、降低库存、提升质量能力、增加经营效益等目标,该系统对所有生产活动中的所有生产环节因素,包括人员、设备、产品等进行实时、不间断、准确的数据通信,并通过预设的流程或逻辑指导产品生产、人机管理和工厂运作。该系统的重点是优化和改善生产活动,减少浪费,提高经济效益。其关键词是精确的实时数据,而这一点是基于事务的 ERP 和 MRP-II 系统没有考虑到的。 从上面可以看出,关于 MES 虽然描述不一,但是核心内容不尽相同:
(1)MES 可以在企业各个信息终端实现双向通信,管理层可以修改和下达逻辑指令到控制层,同样,控制层可以根据预设的需要将生产数据信息实时存储到数据库,用以数据查询、比对和分析。
(2)MES 有较强的及时性,这是系统的核心,抛开这一特点,MES 将毫无价值。这是实现企业动态管理的基础。
(3)MES 数据的准确性是优化和改善活动的基础,这就要求系统的数据库搭建逻辑缜密,生产活动无漏洞,数据传输无差错。
...............................
第三章 KBD 公司 MES 项目实施背景分析 .......................... 15
3.1.1 汽车零部件制造企业的产业特性 .................................... 15
3.1.2 汽车零部件制造企业的生产特征 ...................................... 16
第四章 KBD 公司 MES 项目实施的风险识别.................................... 24
4.1 项目风险识别过程 ............................ 24
4.2 项目风险识别结果 ....................................... 27
第五章 MES 项目的风险评估和风险防范..................................... 31
5.1 基于 FMEA 分析方法的指标权重分析 ................................... 31
5.1.1 风险失效模式的严重度分析 ............................................ 32
5.1.2 失效模式发生度和可探测度分析 ............................. 35
第五章 MES 项目的风险评估和风险防范
5.1 基于 FMEA 分析方法的指标权重分析
本文在表 4.1 中已经通过头脑风暴法、KJ 法以及 likert 评分法例举了 44项风险点。接下来需要对这些风险点进行评估和防范。本文结合笔者在汽配行业的工作经历和经验,将采用 FMEA 分析工具进行阐述。需要说明的是,在后文的阐述中,风险点/项目风险失效模式是同一个概念。
故障模式与影响分析(FMEA)是一种广泛应用的预防性定性分析方法。它列出并研究了产品组件或过程的潜在故障模式,并确定了每种故障模式的影响,以便提前预防和响应。FMEA 应持续评估、演示和改进已识别的失效模式,以逐步优化项目和产品。在实践中,故障模式与影响分析通常用于消除故障原因,将潜在故障或失效消除在萌芽状态。其工作程序如图 5.1。
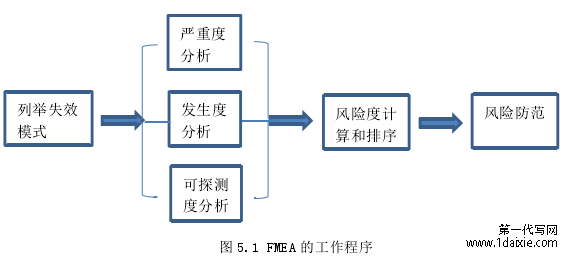
..........................
第六章 结论与展望
6.1 研究结论
MES 项目是 KBD 公司智能制造布局下的代表性项目,鉴于软件类项目风险隐藏性的特点,只有采用科学的管理工具,对风险进行充分识别和评估,采取有效的应对策略和监督执行,项目才能实施中被顺利推进。
本文对 KBD 公司实施 MES 项目的风险管理开展研究,得出的主要结论如下:
(1)由于 MES 项目的成果是一款复杂的功能性产品,其具有开发技术难度高,时间紧迫,人为因素影响大,风险之间互相影响等特点,使得任何形式的风险管理工具在此类项目上的应用都具有较大的参考意义。
(2)MES 项目的风险识别在本项目的研究内容中占有重要地位。风险识别的深入程度,决定了评估的有效性和对策的针对性。本文结合项目实际,通过组建内部由技术人员和管理人员组成的专家队伍,经过头脑风暴的充分挖掘和 KJ法的分类讨论,对项目风险点进行李克特量表打分的方式,筛选出了获得一致认可的必要性风险项目。
(3)本文结合 FMEA 持续性和连续性的特点,运用 FMEA 工具改善项目风险管理过程,针对各类风险,按照其评估结果,根据重点项分析原则提出相应的应对策略,并降低风险值。连续数轮的 FMEA 分析将所列风险的风险度都控制在了比较低的数值。
(4)项目实施中通过风险监控小组,实时监控风险点并提醒责任人在规定时间内完成整改,保证了风险管控的落地执行。
参考文献(略)