第一章 绪论
1.1 研究背景及研究意义
随着计算视觉技术的发展,人们的日常生活以及工业自动化得到了巨大的改善以及迅猛地发展。在工业制造领域,生产自动流水线的出货量越来越受到出产检测效率的影响,尤其在对机械自动化高度依赖的汽车生产自动化流水线上,汽车零件的加工制造环已经实现了几乎无人的水平,但产品的质检环节通常需要由人工完成。而基于计算视觉的无接触检测技术可以有效提高生产率、降低劳动强度,同时避免干扰流水线生产流程或者破坏其物体表面纹理,更加有利于无尘化生产车间的实现。总的来看,基于计算视觉的技术具有非接触性、实时性好、速度快、精度高和易于实现自动化等优点。而且,图像处理、目标识别、目标分割等在计算机视觉领域处于关键地位的经典问题,在工业制造以及生产的各个环节发挥着至关重要的作用,例如在薄片零件尺寸检测系统中的边缘检测[1]、铝合金型材的高温生产过程中的物体检测[2]以及利用图像分割获得准确的零件表面信息[3]等。基于计算视觉的技术在工业制造业中的质量检测环节的应用得到了快速发展。
近几年来随着物体表面三维数据采集设备的发展,以及三维采集精度的提高,计算机视觉的应用扩展到了新的领域,基于三维数据的工业产品表面质量检测受到了学术界和工业界的广泛关注。不同于传统的基于二维图像的表面质量检测技术,其难以分析表面凹凸缺陷以及计算测量尺寸公差、形状公差和位置公差。物体表面的三维数据可以更好地描述大多数表面形状较复杂产品的表面深度信息。基于深度信息,可以更快速准确地定位目标区域在现实世界中的姿态与方位,帮助工业零件生产过程的缺陷的检测与定位,进一步完善工业生产过程的数字化。
.......................
1.2 研究现状
随着智能制造以及工业 4.0的深度融合,计算视觉在工业零件质量检测中发挥着日益重要的作用,与之相关的检测识别技术近几年得到了广泛深入的研究和发展,涉及到精密测控、自动生产线、粮食选优、显微医学操作等与工业生产制造相关的领域。具体到实际应用,有零件装配完整性检测、装配尺寸精度检测、PCB 板检测识别、印刷品检测以及瓶盖检测等。甚至在农业生产以及医药生产领域,计算视觉技术也能用来辅助农产品的品质检测[7,8]以及植被生长情况[9]的判断,或者对药物的运动轨迹进行分析和处理[10],以指导更高效率的农业生产活动和实现对药物的质量管理。总之,生产流程中大部分需要人工参与的质量检测环节已经或者正在逐渐利用计算视觉技术作为辅助工具以达到更高的生产效率。罗菁等[11]对自动化生产过程中的产品表面缺陷问题进行总结,提出基于计算视觉的表面缺陷问题的难点在于缺陷和非缺陷区域的低对比度、噪音以及细微缺陷的相似性。汤勃等[12]阐述并归纳了典型的基于计算视觉的缺陷检测系统的工作原理和基本结构。尹仕斌等[13]对计算视觉技术在现代汽车制造的流程进行了总结,介绍了视觉测量、视觉引导和视觉检测的方法与应用。总的来看,由于计算机视觉在制造业中的广泛使用,与其结合密切的质量检测环节将会得到越来越多的关注。
.............................
第二章 工业零件表面的三维数据采集方法
2.1 3D 视觉传感器
本文中所使用的三维点云由天津微深联创科技有限公司(以下简称微深公司)的编码结构光相机提供。结构光相机的工作原理为将已知的图案,如相线,投射到物体或场景的表面上,利用投影仪投射出具有一定编码规则的图案,通过对投射图案的编码与解码来获取相应匹配点,之后再利用体视测量方法获得物体的深度信息[40]。编码结构光在测量过程中具有高速度、高精度等优点,同时鉴于其属于非接触主动式测量技术,且传感器具有体积小、重量轻等优点[41]。本文采用了基于编码结构光的双目视觉技术对目标工件进行数据采集工作。编码结构光相机的工作基本原理如图 2.1 所示,本文中使用的采集设备实物如图2.2 所示。
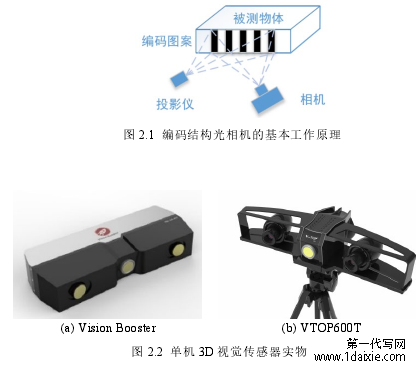
图 2.2 单机 3D视觉传感器实物
2.2 简单形状的工业零件数据
简单形状结构的工业零件在本文中的定义是拥有简单的轮廓、表面几何形状和较为平整的表面等此类易于提取的几何特征。本文以高铁摩擦片作为简单形状的表面质量检测技术的研究对象。高铁摩擦片分为三种型号:A050 型、A040 型和 B050 型。
1.A050 型高铁摩擦片三维数据
A050 型高铁摩擦片的设计图纸、标准模型和扫描数据如图 2.4-图 2.6 所示。设计图纸提供侧视图以及俯视图下的设计尺寸,需要注意的是,并不是所有尺寸值在本文中都需要被测量。因为工件在扫描时基体部分在上,A050 和 A040的上半部分的小圆柱嵌在扫描平台中,所以在实际扫描点云中不会出现。
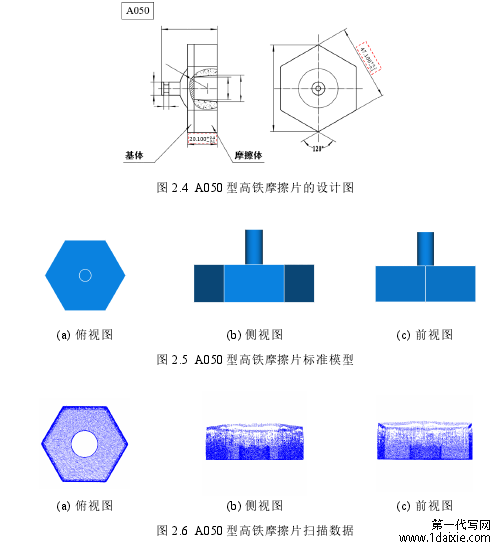
图 2.5 A050型高铁摩擦片标准模型
第三章 简单形状的工业零件的表面质量检测技术.........................14
3.1 表面质量检测任务.............................14
3.1.1 表面质量检测项 .........................................14
3.1.2 表面质量检测项的定义 .........................15
第四章 复杂形状的工业零件的表面质量检测技术..............................43
4.1 表面质量检测任务................................43
4.2 复杂形状的工业零件的表面质量检测方法.............................44
第五章 总结与展望..................................57
5.1 全文总结.................................57
5.2 工作展望........................................57
第四章 复杂形状的工业零件的表面质量检测技术
4.1 表面质量检测任务
在介绍针对石油管螺纹的表面质量检测方法之前,需要对石油管螺纹的检测项以及检测要求进行说明。在本章的检测任务中,输入数据为单帧的石油管螺纹处点云数据和标准模型。针对石油管螺纹的表面质量检测主要为螺纹处的尺寸测量,测量部位是螺距和尺高,螺距为螺纹之间的距离,尺高为螺齿到螺面之间的高度。螺距和尺高的位置如图 4.1(b)所示,在石油管螺纹单帧点云数据的位置如图 4.1(a)所示。
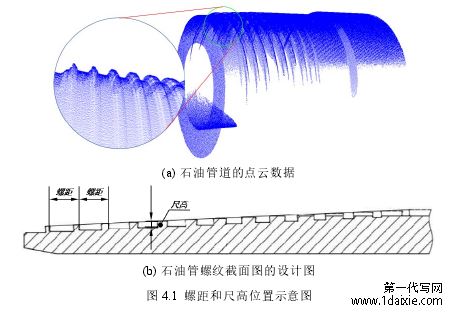
图 4.1 螺距和尺高位置示意图
第五章 总结与展望
5.1 全文总结
在生产制造领域,工业零件的质量检测是十分重要的一个环节,其中包括尺寸测量以及缺陷的检测。本文的主要工作总结如下:
(1)利用 3D 视觉传感器所采集的数据作为输入,本文首先提出并实现了针对于简单形状结构工业零件的表面质量检测方法,并结合实际生产需要,应用于高铁摩擦片的表面质量检测中,包括三种类型摩擦片的对边长度测量、厚度测量以及缺陷区域的检测。在方法中,依据工件的平面特征,使用了较为通用的算法最后设计了针对性的检测方法,例如平面的提取、去除侧面点集、提取有效侧面点以及提取底面交线等步骤,完成了一套高铁摩擦片的检测方法。最后通过与专业技术人员检测结果对比,说明本方法能够以较高的准确率以及效率完成对目标工件指定的表面质量检测,验证了本方法的有效性以及高效率。除此之外,在数据集中的检测结果表明,此方法虽然满足车间流水线的需求,但在面对实际采集数据稀疏的情况时,存在少部分检测失败和漏检的情况。
(2)基于工业零件的标准模型,本文提出一种针对复杂形状结构工业零件的表面质量检测方法,并结合实际生产需要,应用于石油管螺纹的表面质量检测中。其基于一次性的人工标注简化了测量设计的逻辑,并且此方法还包括点云配准、搜索标注点集和特定的尺寸计策略。点云的标注作为前期准备工作不参与实际检测流程中。本方法通过与人工检测结果对比实验,表明在保存点云配准算法的计算结果,也就是保存了待检测点云与标准模型之间的变换矩阵的情况下,此方法具备同人工检测十分接近的结果,但是却有着 9 倍于人工检测的效率。另外,本方法的在尺寸测量设计中的思路不需要设计具有针对性的查找算法对特定区域进行搜索,例如平面和圆。而是概括为计算几何形状之间的空间关系,从而检测方法的设计流程得到了大量的简化,因此具备一定的能力用于一般形状的工业零件的表面质量检测。
参考文献(略)