第一章 引言
1.1 特种加工技术的概念及其意义
特种加工是一种利用化学能、电能、声能、机械能以及光能和热对金属或非金属材料进行加工的方法。它具有传统加工无法比拟的优点:1) 能量密度高,能加工常规切削方法难以加工的材料;代写工学硕士论文2) 作用时间短,热影响小,工件不易变形;3) 可进行细小精密零件加工;4) 无切屑或者粉末状切屑,易于自动处理;5) 加工过程易于自动化。
随着科学技术迅猛地发展,新型材料不断地涌现出来,而有些材料对工件制造的精度要求越来越高,因而对切削加工提出了新的要求。由于受刀具材料性能、结构、设备加工能力的限制,使用传统的切削方法难以完成对高强度、高韧性、高硬度、高脆性、耐高温和磁性等新材料,以及精密复杂或难以处理的形状的加工。为了解决这些加工的难题,目前国内外正在不断开发研究或采用的特种加工技术和方法,并已攻克和解决了一些难以加工的技术关键问题,推动了科技进步,提高了生产效率和产品质量,在工作上发挥了较好的作用。
1.2 特种加工技术的类别及其应用范围
1.2.1 机械特种加工
机械特种加工不同于传统的切削加工方法,而是用机械能或者间接用声能、热能进行加工。可分磨料流动加工、磨料喷射加工、液力加工、低应力磨削、热辅助加工、超声波加工、全成型加工、喷水加工等8 种方法。它适用于切割、穿孔、研磨、抛光、去毛刺、蚀刻、磨削、拉削、镗削和套料等加工范畴。
1.2.2 电气特种加工
电气特种加工是将被加工的金属工件置于直流电场和电解液中产生阴极溶解的电化学反应而对金属材料进行加工的一种方法。通常称为电化学加工(电解加工) 。它有电解液冲刷加工、成型管电解加工、电化学削平加工、电化学珩磨加工、电化学车削加工、电化学去毛刺加工、电化学放电磨削加工、电化学加工、电化学抛光加工等10 种方法。它适用于磨削、成型、去毛刺、车削、珩磨、抛光等加工范畴。
1.2.3 热特种加工
热特种加工是用电子束、激光束、等离子束、电火花放电产生热量来熔蚀金属而达到加工目的。它有电子束加工、电火花磨削、电火花成型加工、电火花切割、电火花线切割、激光加工、等离子束加工等8 种方法。它适用于钻孔、成型、磨削、车削、切割、开割、划线等加工范畴。
1.2.4化学特种加工
化学特种加工是用热化学方法、化学腐蚀方法进行加工的。它有化学加工、光化学加工、热化学加工、电抛光等4 种方法。它适用于削平、抛光、腐蚀、去毛刺和飞边等加工范畴。
1.3 特种加工技术现状及实际应用
1.3.1 机械特种加工
在一般采用金属切削刀具难以加工的场合,采用机械特种加工。它是借助于水、磨料、超声波、热能等,实施对工件进行的精密加工。
1.3.2 电气特种加工
电气特种加工又称为电解加工。它是特种加工技术中重要的方法之一,是利用金属在电解液中的电化学阳极溶解来将工件加工成形的。电解加工成功应用于锻模、齿轮、花键、高温合金叶片等机械零件成型加工,采用电解液冲刷加工和成型管电解加工可以加工孔径0. 2 mm~5 mm ,也可以加工异型孔的小深孔机械零件。
1.3.3 热特种加工
电子束、激光束、等离子束、电火花放电加工等热特种加工,是特种加工应用较为普通的一种技术,电火花放电加工更为成熟更为普及,也是机械加工不可缺少的一项技术。
1.3.4 化学特种加工
化学特种加工是一种使用面较窄的特种加工技术,它是在工件表面产生化学反应,使用金属腐蚀溶解而改变工件尺寸和形状,具有加工周期短、变换产品快、工艺性能好等特点,它主要用于印刷线路板制造,这种使用场合称为化学铣切。另一种化学加工方法是把工件暴露在高温、腐蚀性气体中来切除材料。
1.4 电火花加工的发展及现状
电火花加工又称放电加工,在20世纪40年代开始研究并诼步应用于生产,电火花加工是基于脉冲放电的电蚀原理,靠放电时产生的高温把金属蚀除下来。
1.4.1 电火花加工技术的发展趋势与工艺进展
目前电火花加工技术的研究与发展趋势主要表现在以下几个方面:
(!)加工微细化 随着工程技术领域对微型机械的迫切需求,微细加工已不再是微电子机械技术的代名词。微细电火花加工技术的应用领域已经从简单的轴孔加工逐步拓展到微三维结构型腔的制作中。微细电火花加工技术有望成为三维实体微细加工的主流技术之一。
(2) 加工装置的微小型化 由于电火花加工中工具电极与工件之间没有宏观作用力,因此,将电火花加工装置、尤其是电极驱动机构进行微小型化,使电极进给驱动系统的惯性得以大幅度减小,必将更好地发挥电火花加工技术的工艺特点。
(3) 新型元器件的成功应用 不断地吸收现代科技发展的精髓是任何制造技术得以生存和发展的前提。目前一些新型开关元件如IGBT ,大规模集成电路芯片如FPGA、DSP ,新型压电材料等均已在电火花加工机床的脉冲电源、控制系统及驱动装置上得到了极为成功的应用,大大地提高了EDM的加工性能与工艺指标。
(4) 硬件软件化 软件在电火花加工机床上所占的比重日趋增大。这一趋势表明,一些新的软件平台、数控技术有可能很快地融入电火花加工技术中,从而将极大地提高电火花加工技术的快速响应能力。
(5) 现代制造模式的渗透 人工智能技术、网络制造、绿色制造、敏捷制造等新概念正逐渐渗透到电火花加工领域中。
(6) 新工艺的出现 借助现代化的研究手段,人们对电火花加工技术的研究正向更深层次发展,新的工艺方法不断涌现,电火花加工技术的应用领域正在拓宽。
1.4.2 电火花加工的最新工艺进展
任何一种实用的制造技术最终都要体现在工艺上,工艺方法的不断完善与实用化表征该技术的生命力与存在价值。
电火花加工的最新工艺进展主要体现在如下几个方面:
1 微细电火花加工
2 气中放电加工
3 混粉工作液电火花镜面加工
4 非导电材料的电火花加工技术
5 电火花表面处理及毛化技术
6 电火花铣削加工技术
从以上电火花加工技术的发展趋势和工艺进展情况不难看出,随着科技发展和社会进步,电火花加工技术必将在未来的制造领域发挥更大的作用。
图1-1为电火花加工机床
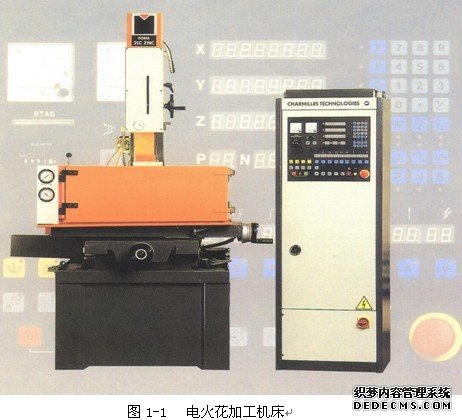
图1-1 电火花加工机床
第二章电火花加工的机理及应用
2.1电火花加工的原理
电火花加工是基于脉冲放电的电蚀原理;工具电极与工件电极在绝缘工作液体中靠近并接通脉冲电源,极间电压将在两极间“相对最近点”电离击穿,形成脉冲放电产生的高温代写工学硕士论文来蚀除多余的金属,以达到对零件的尺寸、形状及表面质量加工到预定的技术要求。工具电极和工件被加工表面间的放电间隙通常为几微米至几百微米,靠工具电极的自动进给和调节装置控制;放电是脉冲性放电,共延续时间为10秒—10秒;火花放电必须在一定绝缘的工作介质(通常为液体)中进行,工作液为流动的流体,把电火花加工过程中产生的金属小颗粒等电蚀产物从放电间隙中排除出去。电火花放电的机理简单地说是四个连续的阶段。
(1)介质击穿:极间介质的电离、击穿、形成放电通道;
(2)能量转换:介质热分解、电极材料熔化、气化;
(3)蚀除产物的抛出。
(4)极间介质的消电离。
它是电场力、磁力、热力、流体动力、电化学等综合作用的一个微观过程,也是复杂的过程。
2.1.1 极间介质的电离、击穿、形成放电通道
液体介质中不可避免地含有某种杂质(如金属微粒、碳粒子、胶体粒子等),也有一些自由电子使介质呈现一定的电导率。在电场作用下,这些杂质将使极间电场更不均匀,当阴极表面某处的电场强度增加到10万V/mm时,就会产生场致电子发射,由阴极表面向阳极逸出电子。在电场力作用下负电子高速向阳极运动并撞击工作液介质中的分子或中性原子,产生碰撞电离。形成带负电的粒子(主要是电子)和带正电的粒子(正离子),导致带电粒子雪崩式增多,使介质击穿而形成放电通道。放电通道是由数量大体相等的带正电(正离子)和带负电粒子(电子)以及中性粒子(原子或分子)组成的等离子体。关于通道的结构,一般认为是单通道,即在一次放电时间内只存在一个放电通道。图2-2为电离准备阶段的模型图,它分为建立电场、极化搭桥以及电子发射三个分阶段,分别对应图2-2中(a)、(b)、(c)。
图2-2 电离准备阶段的模型图
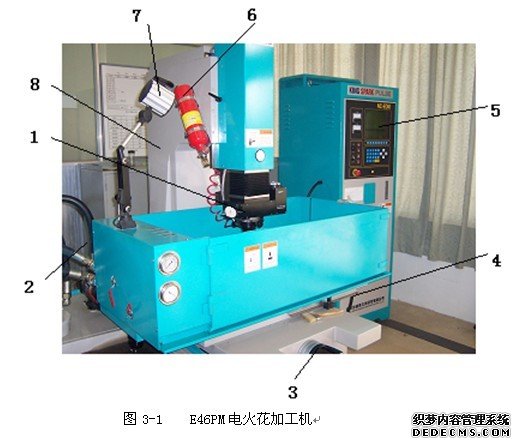
2.1.2 介质热分解、电极材料熔化、气化
极间介质一旦被电离、击穿、形成放电通道后,脉冲电源使通道间的电子高速奔向正极,正离子奔向负极。电能变成动能,动能通过碰撞又转变为热能。于是在通道内、正极和负极表面分别成为瞬时热源,分别达到很高的温度。通道高温首先把工作液介质气化,进而热裂分解气化。如煤油等碳氢化合物工作液,则高温后裂解为氢气(约占40%)、乙炔(约占30%)、甲烷(约占15%)、乙烯(约占10%)和游离碳等。如水基工作液则热分解为氢气、氧气的分子甚至原子等。正负极表面的高温除使工作液气化、热分解气化外,也使金属材料溶化、直至沸腾气化。这些气化后的工作液和金属蒸气,瞬时间体积猛增,迅速热膨胀,就像火药爆炸后那样具有爆炸的特性。观察电火花加工过程,可以见到放电间隙间冒出许多小气泡,工作液逐渐变黑,和听到轻微而清脆的爆炸声。主要靠此热膨胀和局部微爆炸,使溶化、气化了的电极材料抛出蚀除。
2.1.3 电极材料的抛出
通道和正负极表面放电点瞬时高温使工作液气化和金属材料溶化、气化热膨胀产生瞬时压力。通道中心的压力最高,使气化了的气体体积不断向外膨胀,形成一个扩张的“气泡”,气泡上下内外的瞬时压力并不相等,压力高处的熔融金属液体和蒸气,就被排挤抛出而进入工作液中。下图图2-3为消离抛出阶段的模型图。图中(a)为通道崩溃和气泡扩展,(b)为气泡收缩,(c)为过程结束。
图2-3 消离抛出阶段的模型图
2.1.4 极间介质的消电离
极间介质的消电离即放电通道中的带电粒子复合为中性粒子,恢复本次放电通道处间隙介质的绝缘强度,以免总是重复在同一处发生放电而导致电弧放电,这样可以保证按两极相对最近处或电阻率最小处形成下一级击穿放电通道。
2.2 电火花加工的特点
(1)可以加工任何硬、脆、韧、软、高熔点的导电材料。材料的可加工性主要取决于材料的导电性和熔点、沸点、比热容、电阻率等,而几乎与其力学性能(硬度、强度等)无关。可以用软的工具(如纯铜或石墨)加工坚硬的工件。
(2)加工时无宏观的机械切削力,可以加工小孔、窄缝以及各种复杂截面的型孔、曲线孔型腔等以及薄壁零件的加工,也适于精密加工。
(3)脉冲参数可以任意调节,以便在同一台火花加工机床上连续进行粗、半精、精加工,提高生产率。
2.3电火花加工的局限性
(1)主要用于金属等导电材料,但在一定的条件下也可加工半导体和非导体材料。
(2)一般情况下加工速度较慢,生产率不高,但最新的研究表明,在特殊水基不燃性工作液中电火花加工有很高的生产率,可是只用在粗加工过程中。
(3)会损耗工具电极,影响成形精确度。
随着科学技术的发展,具有复杂三维型面的难加工材料的应用越来越广泛,普通的机械加工难以满足要求,而特种加工中的电火花加工具有成形精度高,可加工三维曲面的任何导电性材料的特性,在特种加工中具有重要地位,在现代制造业中有重要应用。
2.4电火花加工的应用
由于电火花加工有许多传统切削加工无法拥有的优点,因此其应用领域遍及机械(特别是模具制造)、航空、航天、军械制造、电子、电机电器、精密机械、仪器仪表、汽车、轻工等行业。加工的尺寸范围从几微米的小孔、小轴、缝到几米的超大型模具和零件。
但任何事情总是一分为二的,它有优势也有劣势,电火花加工也存在一些缺陷。
反映电火花加工工艺效果的主要指标有:加工精度、表面质量、加工速度和电极损耗比等。电火花加工参数一般分为电参数和非电参数,它们相互影响,关系错综复杂。加工参数对加工速度、加工精度和表面质量的主要影响表现在以下几个方面:
(1) 加工速度,是指一定规准下单位时间内工件被蚀除的体积或质量。它主要受电参数、极性效应、工件材质、工作液种类等因素的影响。
(2) 影响加工精度的主要因素有:机床本身精度、工具电极的尺寸和形状精度、工具、工件装夹误差、放电间隙、电极损耗等。
(3)影响电火花加工表面质量的主要因素可从表面粗糙度、加工表面层的组织变化、表面微裂纹3个方面来分析。
下表表 2-1为电火花加工工艺方法分类
表2-1电火花加工工艺方法分类
类别
|
工艺方法
|
特点
|
用途
|
备注
|
1
|
电火花穿孔成形加工
|
1.工具和工件间主要只有一个相对的伺服进给运动
2.工具为成形电极,与被加工表面有相同的截面或形状
|
1. 形腔加工:加工各类型腔模及各种复杂的形腔零件
2 .穿孔加工:加工各种冲模,挤压模、粉末冶金模、各种异形孔及微孔等
|
约占电火花机床总数的3%
|
2
|
电火花线切割加工
|
1 .工具电极为顺电极丝轴线方向移动着的线状电极
2. 工具与工件在两个水平方向同时有相对伺服进给运动
|
1. 切割各种冲模和具有直纹面的零件
2 下料、截割和窄缝加工
|
约占电火花机床总数的60%
|
3
|
电火花内孔、外圆和成形加工
|
1 .工具与工件有相对的旋转运动
2. 工具与工件间有径向和轴向的进给运动
|
1.加工高精度、表面粗糙度值小的孔
2 .加工外圆、小模数滚刀等
|
约占电火花机床总数的60%
|
4
|
电火花同步共轭回转加工
|
1.成形工具与工件均作旋转运动,但二者角速度相等或成整数倍,相对应接近的放电点可有切向相对运动速度
2 工具相对工件可作纵、横向进给运动
|
以同步回转,展成回转、倍角速度回转等不同方式,加工各种复杂型面的零件
|
约占电火花机床总数不足1%
|
5
|
电火花高速小孔加工
|
1 采用细管电极,管内冲入高压水基工作液
2 细管电极旋转
3 穿孔速度极高(60mm\min)
|
1线切割预穿丝孔
2 深径比很大的孔,如喷嘴等
|
约占电火花机床总数的2%
|
6
|
电火花表面强化
|
1 工具在工件表面上振动
2 工具相对工件移动
|
1 模具刃口,刀、量具刃口表面强化和镀覆
2 电火花刻字、打印记
|
约占电火花机床总数的2%-3%
|
第三章 电火花加工实验仪器
图3-1 E46PM电火花加工机
图3-1 实验的型号为E46PM电火花加工机。台面尺寸650mm*400mm,工作台行程400mm*300mm,Z轴伺服行程200mm。图中,1为主轴头,2为电火花机床的工作液供给系统, 3和4分别为X轴和Y的进给拖板,5为台湾生产的电火花脉冲电源发生器,6为灭火器,7为照明灯,8为机床床身。
电火花穿孔成型加工机床主要由主机(包括自动调节系统的执行机构)、脉冲电源、自动进给调节系统、工作液净化及循环系统几部分组成。
图3-2 面板
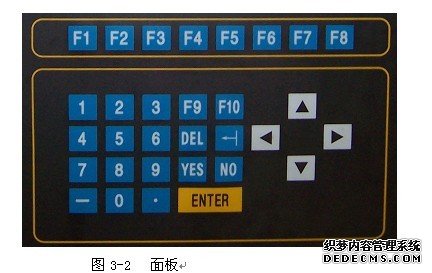
3.1 机床控制面板
3.1.1操作面板
面板介绍E46PM使用F1-F10功能键及数字键0-9和小数点,各按键说明如下:
1. 功能键F1-F10设定和执行使用功能;
F1:单节放电设定 F2:自动放电设定
F3:程式编辑 F4:位置归零
F5:位置设定 F6:找中心点
F7:放电条件设定 F8:参数设定
F9:放电计时归零 F10:放电参数自动匹配
2. 数字键0-9输入数字用,包括坐标位置及EDM参数;
3. ENTER键:确认输入键;
4. YES/NO:询问回答键(是/不是);
5. 退后键:用于删除错误输入;
6. 移动键:用于程式编辑及轴向选择;
7. — 键:输入为负值。
8. 游标:移动游标指定的轴向
9. 游标:移动游标指定的轴向
试验中用F1-F10功能键实现各种功能的切换,用8键实现各种参数的转换,用9键实现参数值的修改。
3.1.2 参数视窗
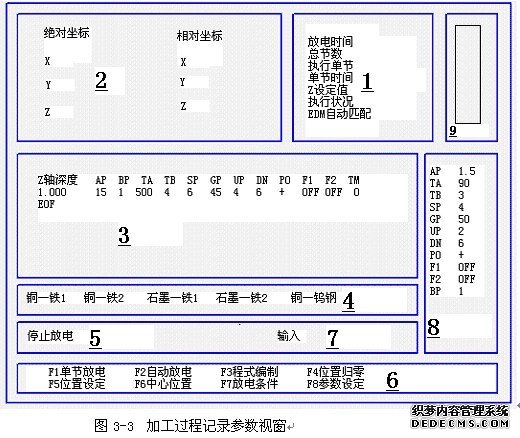
图3-3 加工过程记录参数视窗
1. 状态显示视窗:显示执行状态,包括计时器,总节数执行单节及Z轴设定值;
2. 位置显示视窗:显示各轴的位置包含绝对坐标及相对坐标X、Y、Z三轴;
3. 程式编辑视窗:程式编辑操作(自动加工专用);
4. 加工材质视窗:显示所选之加工材料;
5. 讯息视窗:显示加工状态及讯息;
6. 功能键显示视窗:F1—F8操作按键;
7. 输入视窗:显示输入值;
8. EDM参数显示视窗:EDM参数操作更改;
9. 加工深度视窗:以图示显示加工深度。
3.1.3 指示灯与报警装置
图3-4 机床的指示灯
机床的四个红灯(如图3-4)由上到下依次是:1深度到达指示灯,2碰边指示灯,3防火指示灯,4积碳指示灯。各指示等的功能如下:
1.深度到达指示:指示灯亮表示Z轴的深度到达,蜂鸣器持续报警,将Z轴上移可以消除。
2.碰边指示:指示灯亮表电极与工作物接触,接触时蜂鸣